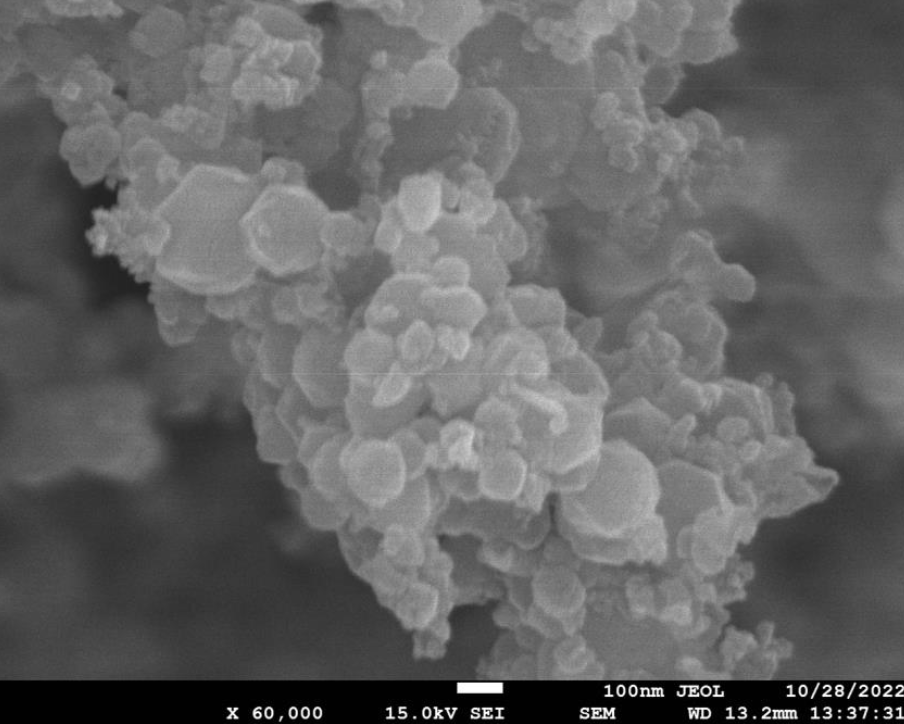
Welcome to our exploration of turbostratic graphene nanoparticles. Join us as we examine the details of this exciting technology, which is setting new standards in the nanomaterials industry.
An In-depth Look into Graphene Nanoparticles
You may have noticed the rising interest in graphene-based nanomaterials and a surge in products containing graphene being sold. Their unique properties make them well suited for use in a variety of applications, from electronics, polymers, composites, and concrete to energy storage. While there are many types of graphene and a variety of synthesis methods, turbostratic graphene nanoparticles synthesized through bottom-up methods could have great potential due to its high quality, scaleability, and commercially viable cost.
The Fundamentals of Graphene Nanoparticles Synthesis and Their Industrial Application
Production of graphenes traditionally involve top-down synthesis methods that break down graphite through chemical and mechanical exfoliation. Challenges from variability in nanoparticle quality stemming from natural graphite sources and processing methods hindered commercialization.
A potential solution, rapid pyrolysis otherwise known as detonation synthesis presents an intriguing alternative. By precisely controlling precursor ratios during the ignition and combustion of hydrocarbon, oxygen, and hydrogen gases, the bottom-up method produces high-quality turbostratic graphenes and hydrogen. This novel class of carbon nanomaterials stands out due to its remarkable consistency and reduced production costs when compared to carbon nanotubes and traditional graphenes.
Compared to other multilayer graphene structures, turbostratic graphene layers have a distinctive stacking arrangement. Multilayer graphene exhibits an ordered stacking pattern, while turbostratic graphene introduces rotational disorder, resulting in a random orientation of carbon layers. Each layer in turbostratic graphene maintains its distinct electronic properties, leading to excellent electrical conductivity. This distinctive characteristic makes turbostratic graphene an appealing material for applications requiring multilayer graphene while upholding superior electrical performance.
Traditional Top-Down vs. Bottom-Up Graphene Synthesis Methods
Traditional Top-Down Synthesis of Graphenes. Graphite, a naturally occurring form of crystalline carbon, is traditionally broken down to the nanoscale to produce graphenes thru chemical and mechanical exfoliation methods, a process known as top-down synthesis. While this method might appear simple, it often requires several key compromises. The quality of graphene nanoparticles can vary from batch to batch and requires significant labor and production inputs, increasing production costs.
Graphite can be converted to graphene by intercalating different chemical species between the graphite layers, creating graphite intercalation compounds (GIC) which increases the interlayer distance, altering it’s properties and influencing electronic coupling between layers. Various intercalants result in GIC with distinct properties suitable for applications in electrical, thermal, and magnetic performance. Chemical exfoliation typically adds surface functional groups to the product which may be undesirable and the high costs associated with chemical handling, processing, storage, and disposal must be factored into the graphene’s price. The multi-step nature of chemical exfoliation processes requires subsequent treatments for reduction of functional groups further increasing its cost.
Mechanical exfoliation, the most commonly used top-down method, involves overcoming Van der Waals forces to exfoliate graphite layers into graphene. This method has its challenges, including the high amount of defects and the subsequent re-agglomeration of the graphene layers. Top-down approaches are typically characterized as complex processes with low yields. Ball milling and sonication are often used, with sonication being widely preferred for mechanically separating graphite. The expensive milling machines historically used in graphene production have been plagued by frequent downtime and costly repairs.
Pyrolysis can be both a top-down and bottom-up synthesis method. Top-down pyrolysis offers a scalable and straightforward process for graphene production. A carbon source, often biomass or graphite is rapidly pyrolysed and repeatedly washed with deionized water. The suspended solid is then vacuum filtered and dried in a vacuum oven. Top down pyrolysis is limited by low yield and impurities in the final product.
Chemical reduction of graphite oxide produces graphene flakes from nanometer to micrometer size. Reduction can be achieved through chemical or thermal treatments. It is important to consider that graphene obtained through chemical methods may exhibit more surface defects and lower purity levels.
To summarize, the examined top-down methods present various advantages and limitations. Chemical exfoliation has high costs of chemical handling and multi-step processes, mechanical exfoliation faces challenges of high defects and re-agglomeration. Intercalation offers a means to modify graphene’s properties, while chemical reduction of graphite oxide provides graphene flakes of different sizes. Further advancements in these methods will drive commercialization and widespread the use of graphene materials.
Bottom-Up Graphene Synthesis
Bottom-up synthesis assembles carbon molecules obtained from alternative sources into graphene offering a promising alternative to traditional top-down methods. The approach provides greater precision in controlling the size and number of layers in graphene nanoparticles. Typical bottom-up methods include growth from transition metal/carbon melts, chemical vapor deposition (CVD), epitaxial growth, and now rapid pyrolysis also know as detonation synthesis.
Metal/carbon melts are a simple method for synthesizing different forms of carbon, such as graphite, few layer graphene (FLG), and single layer graphene (SLG). It involves placing a carbon source, like graphite powder, in contact with a transition metal and heating it at high temperatures until the metal melts. As carbon dissolves in the molten metal, the temperature is lowered to precipitate the carbons. The resulting precipitate can be skimmed off to obtain graphenes. The choice of transition metal is critical for this process. Nickel is the most often used metal due to its non-raman active properties. It yields high-quality graphene. Ruthenium and iridium are also usable metals, but the quality of graphene obtained from them is not as good as that achieved from nickel and copper.
Epitaxial growth of graphene on a silicon carbide (SiC) substrate allows for the production of thin graphene films, making it suitable for applications in transistors and circuits. Graphene is obtained through heat treatment of SiC at 1100 °C, resulting in epitaxial graphene. The size of graphene flakes is dependent on the size of SiC wafers, and the surface of SiC influences the thickness, mobility, and carrier density of the graphene produced. This method has the advantage of producing thin graphene films suitable for transistors and circuits. However, its limited by the high production cost associated with expensive SiC substrates and low yield. While epitaxial graphene exhibits desirable properties such as weak anti-localization and temperature-independent mobility, it falls short of the exceptionally high mobility achieved by exfoliated graphene.
Graphene growth on nickel and copper films using chemical vapor deposition (CVD) is a popular method. Both methods utilize high temperatures and carbon-containing gases such as methane to deposit carbon on the surface, resulting in graphene formation. The CVD method on nickel films allows for the growth of single-layer graphene, while copper substrates produce multilayer graphene. Control of the growth conditions and the choice of carbon-containing gases contribute to the quality and scalability of graphene production.
Rapid pyrolysis (detonation) synthesis for graphene nanoparticles presents an interesting option. By precisely controlling precursor ratios during the rapid ignition and combustion of hydrocarbon, oxygen, and hydrogen gases in a specially designed chamber, high quality turbostratic graphenes and hydrogen are produced. What sets this new class of carbon nanomaterial apart from its predecessors such as CNTs and traditional graphenes is its consistency and low production costs. Capable of synthesizing turbostratic graphene with fewer defects and without functional groups that can alter graphene’s desirable properties, this low energy and highly scaleable process produces pristine graphenes in sufficiently large volumes to drive costs down to commercially viable levels and signifies an important step forward in graphene production.
Detonation synthesis allows for more precise control of nucleation and growth when synthesizing graphene nanoparticles. This is a key strength of bottom-up synthesis and detonation synthesis specifically. This new approach provides an avenue for producing smaller, high-quality turbostratic graphene nanoparticles, at commercially viable pricing.
In summary, traditional top-down synthesis methods for graphene nanoparticles present certain challenges and compromises, such as variable nanoparticle quality, high production costs, and complex processes. On the other hand, bottom up methods offer a promising alternative. Metal/carbon melts, epitaxial growth on SiC substrates, chemical vapor deposition on nickel and copper films, and now rapid pyrolysis provide more precise control over graphene production. Detonation synthesis produces high-quality turbostratic graphenes with consistency and lower production costs. By addressing the limitations of traditional approaches, detonation synthesis represents a significant advancement in graphene production, with the potential for widespread commercial adoption.
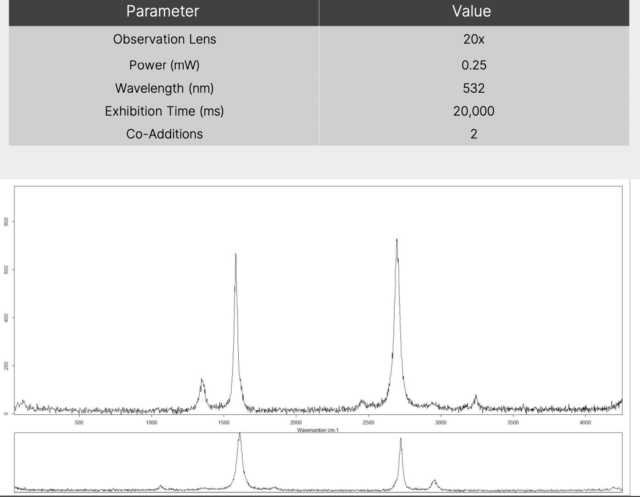
Cost-Benefit Analysis
A comparison of costs and product benefits between traditional top-down synthesis and bottom-up synthesis methods reveals that despite the versatility of top-down synthesis, the lack of precise control over purity and defects poses challenges for product quality and higher production costs reduce commercial viability.
In contrast, bottom-up methods such as detonation synthesis offer more precise control over graphene synthesis. This enables the production of high-quality graphene materials with desirable properties, paving the way for advancements in graphene technology and commercial applications. It’s also less energy intensive. The production chamber is filled with carbon and oxygen-containing gases mixed at precise molar ratios, and the rapid pyrolytic reaction is initiated with a single spark. This results in substantial savings in costs compared to top-down approaches or other bottom-up approaches like CVD.
Detonation synthesis not only produces consistent, high-quality graphene nanoparticles but it improves control over the graphene’s size and number of layers at reduced cost.
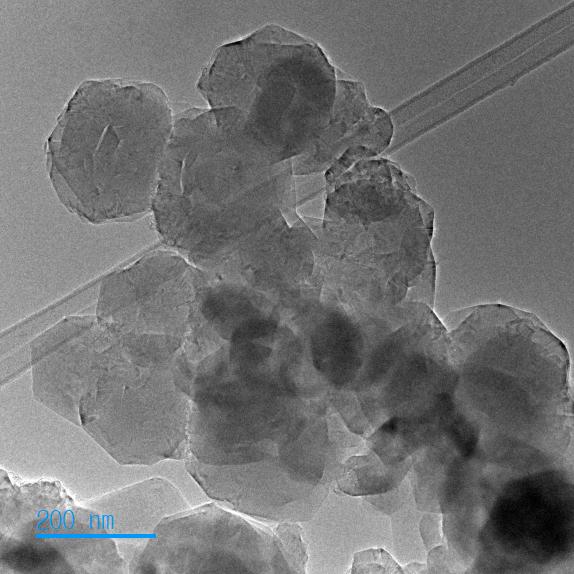
The Importance of Quality in Graphene Nanoparticle Production
Addressing Graphene Customer Concerns
As the graphene industry continues to evolve, customers have encounter a variety of challenges. By overcoming these challenges we are working to offer solutions that enhance the overall customer experience.
Some common customer pain points are below.
Inconsistent Quality: Inconsistent quality can impact product performance and customer satisfaction. We understand that you need graphene nanoparticles that deliver consistent performance. Detonation synthesis may potentially provide a better solution.
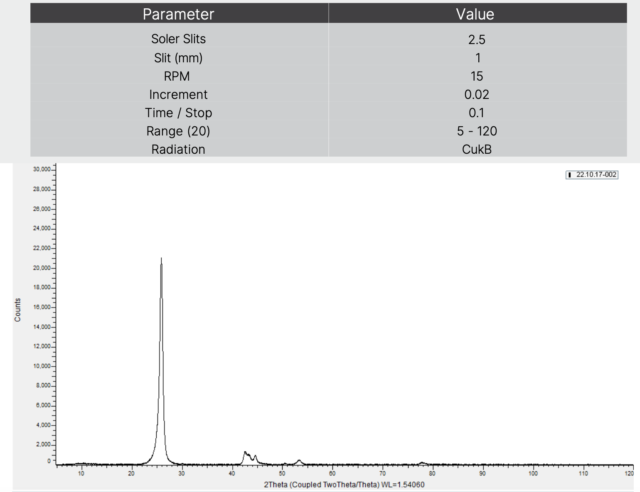
Dispersion: Dispersion of graphene nanoparticles is critical to improve your products’ performance. Agglomerated nanoparticles can create weak spots or voids in commercial applications. Fortunately, the smaller, high-quality turbostratic graphene nanoparticles produced by detonation synthesis are easier to disperse because of the random relative rotation between layers and increased interlayer spacing.
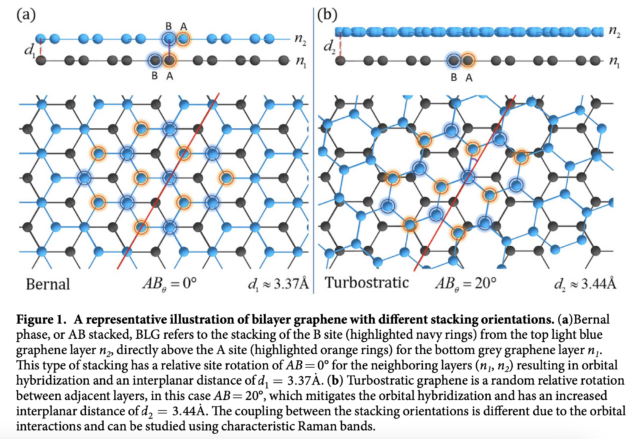
Price: Thanks to the lower production costs realized by the detonation synthesis method, we can deliver high-quality graphene nanoparticles at commercially viable prices, facilitating innovation without straining your budget.
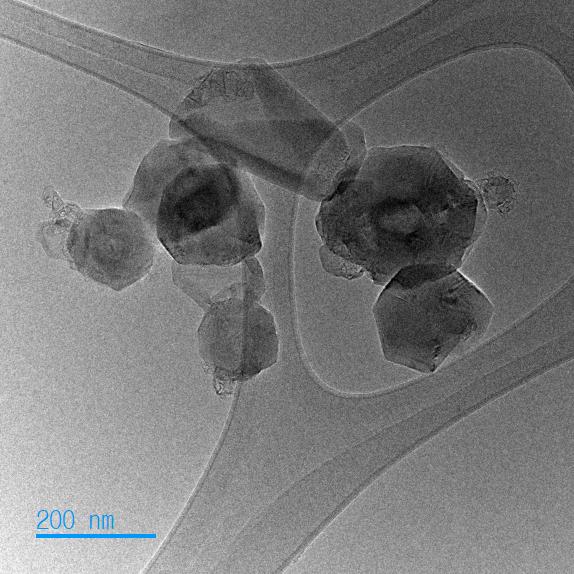
Building Partnerships for a Brighter, Sustainable Future
The future of graphene nanoparticle production is promising, particularly with advancements in synthesis methods like detonation synthesis. With better control over the quality, size, and number of layers, graphene nanoparticles can meet the specific needs of various industries more effectively and affordably. Our focus remains on delivering high-quality products, driving innovation, promoting sustainability, and building strong relationships with our customers. Together, we can chart a path towards a brighter, more sustainable future.
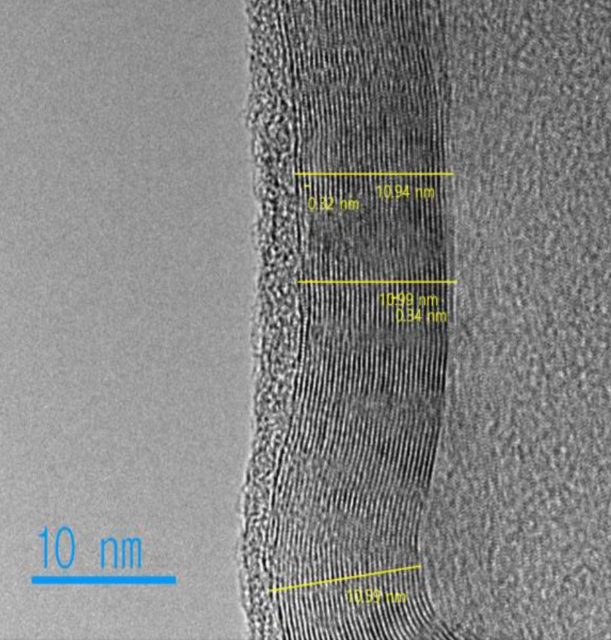
Try our turbostratic graphene product below.
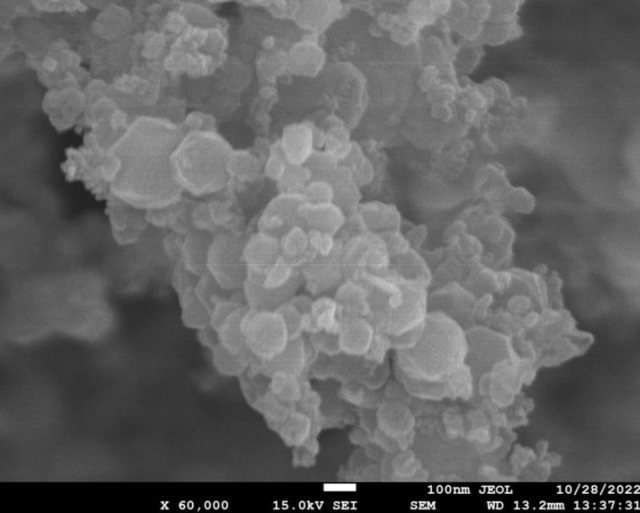
Graphene Nanoparticles Conductive Additive
Graphene Nanoparticles Conductive Additive are perfect for many applications in conductive inks, polymers, concrete, batteries, sensors, fuel cells and many more. Great for applications requiring high conductivity. Fully synthetic and featuring a scaleable low cost and high volume synthesis method. Lab-based tests have shown 30% improvement in concretes compressive strength, and up to 70% improved performance with polymers. Outperforms several other carbon nanomaterials when incorporated into epoxy blends. Great for improving thermal, corrosive, and abrasive properties for industrial applications. Sold by the Kg and tons. Ask for commercial pricing today!
References
[1] Kim, K. S., et al. (2009). “Large-scale pattern growth of graphene films for stretchable transparent electrodes.” Nature 457(7230): 706-710.
[2] Narita, A., et al. (2014). “New advances in nanographene chemistry.” Chemical Communications 50(67): 9279-9282.
[3] Greer, J. R., et al. (2019). “Emerging Materials for 3D Printing and High-Performance Composites.” ACS Central Science 5(7): 1129-1137.
[4] Zhang, X., et al. (2015). “Mechanical properties and applications of graphene, a theoretical review.” Journal of Nanomaterials 2015: 15.
[5] Jacobberger, R. M., et al. (2017). “Direct oriented growth of armchair graphene nanoribbons on germanium.” Nature Communications 8(1): 1-7.
[6] Vadukumpully, S., et al. (2011). “Graphene synthesis and assembly for transparent conductive films: A review.” Journal of Colloid and Interface Science 363(1): 1-15.
[7] Mahmoudi, T., et al. (2017). “Graphene-based nanomaterials for tissue engineering in the dental field.” Nanomaterials 7(6): 131.
[8] Behabtu, N., et al. (2013). “Spontaneous high-concentration dispersions and liquid crystals of graphene.” Nature Nanotechnology 8(6): 406-411.
[9] Usachov, D., et al. (2016). “Bottom-Up Synthesis of Graphene Nanoribbons on Metal Surfaces: A New Trend in Graphene Research.” Journal of Surface Investigation. X-ray, Synchrotron and Neutron Techniques 10(1): 217-223.
[10] Yakobson, B. I., et al. (2010). “Dislocations in bilayer graphene.” Physical Review Letters 105(23): 235502.
[11] Kim, Y., et al. (2015). “Growth of high-crystalline, single-layer graphene on a solid carbon source.” Nano Letters 15(10): 6829-6835.
[12] Alava, T., et al. (2018). “Carbon-based materials and their potentiality for MRSA eradication: The light at the end of the tunnel.” Advances in Colloid and Interface Science 254: 39-51.
[13] Zan, R., et al. (2012). “Scanning tunnelling microscopy of suspended graphene.” Nanoscale 4(9): 3065-3068.
[14] Emtsev, K. V., et al. (2009). “Towards wafer-size graphene layers by atmospheric pressure graphitization of silicon carbide.” Nature Materials 8(3): 203-207.
[15] Fujita, D., et al. (1996). “Novel Nano-Particles: Cluster-Assembled Materials.” Journal of Computer-Aided Materials Design 3(2-3): 123-134.
[16] Wu, Z. S., et al. (2010). “Synthesis of graphene sheets with high electrical conductivity and good thermal stability
[17] Kim, Y., et al. (2015). “Growth of high-crystalline, single-layer graphene on a solid carbon source.” Nano Letters 15(10): 6829-6835.
[18] Alava, T., et al. (2018). “Carbon-based materials and their potentiality for MRSA eradication: The light at the end of the tunnel.” Advances in Colloid and Interface Science 254: 39-51.
[19] Zan, R., et al. (2012). “Scanning tunnelling microscopy of suspended graphene.” Nanoscale 4(9): 3065-3068.
[20] Emtsev, K. V., et al. (2009). “Towards wafer-size graphene layers by atmospheric pressure graphitization of silicon carbide.” Nature Materials 8(3): 203-207.
[21] Fujita, D., et al. (1996). “Novel Nano-Particles: Cluster-Assembled Materials.” Journal of Computer-Aided Materials Design 3(2-3): 123-134.
[22] Garlow, J. A. et al. Large-Area Growth of Turbostratic Graphene on Ni(111) via Physical Vapor Deposition. Sci. Rep. 6, 19804; doi: 10.1038/srep19804 (2016).
[23] Agbolade Lukman Olatomiwa et al Graphene synthesis, fabrication, characterization based on bottom-up and top-down approaches: An overview 2022 J. Semicond. 43 061101